The Duravant family of operating companies serve the food processing, packaging and material handling segments.
Mastering Industrial Filling Machines for Maximum Efficiency and Cost Savings
In today's competitive manufacturing landscape, achieving optimal efficiency and cost savings is paramount for businesses looking to thrive. One of the key components in streamlining production processes is the industrial filling machine. These machines play a crucial role in a variety of industries—ranging from food and beverage to pharmaceuticals—by ensuring the precise and swift filling of products into containers. As companies strive to enhance their operations, mastering the technology and functionality of industrial filling machines becomes essential.
Understanding the intricacies of industrial filling machines can lead to significant advancements in productivity and profitability. By leveraging advanced features and implementing best practices in their use, manufacturers can minimize waste and reduce operational costs. This blog aims to provide valuable insights into the various types of industrial filling machines, their benefits, and strategies for maximizing their performance in order to achieve the highest levels of efficiency and cost-effectiveness. Join us on this journey to discover how mastering industrial filling machines can transform your production capabilities.
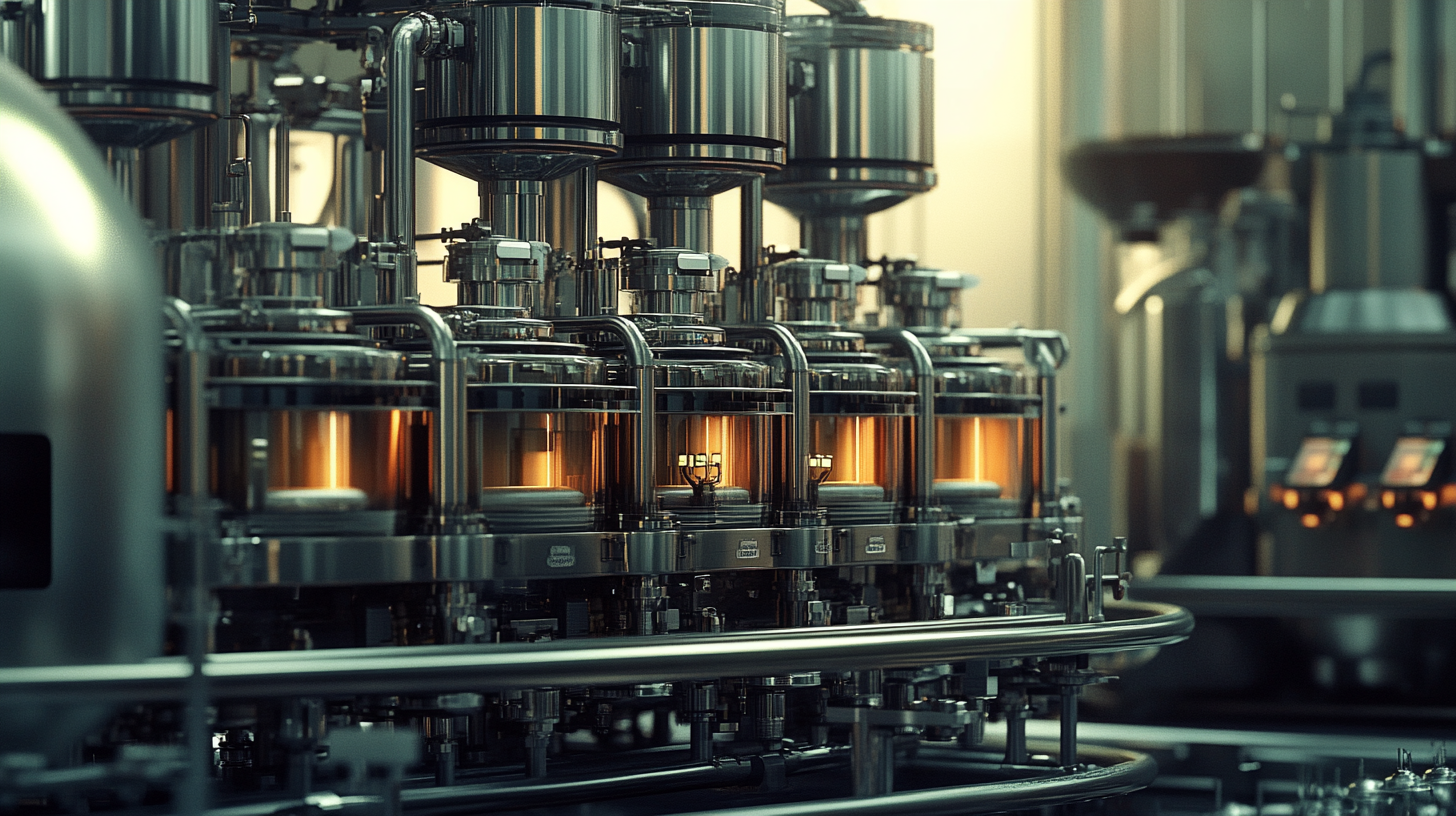
Understanding the Different Types of Industrial Filling Machines
Understanding the Different Types of Industrial Filling Machines
When it comes to maximizing efficiency in manufacturing, the type of industrial filling machine employed plays a crucial role. There are several types of filling machines, each designed to cater to specific industries and products. For instance, volumetric filling machines measure the volume of a product and dispense it accordingly. These machines are ideal for liquids, granules, and powders, providing consistent and precise fills that are essential for maintaining product quality.
Another popular type is gravimetric filling machines, which weigh the product before dispensing. This method ensures high accuracy, making it perfect for applications where precise measurements are critical, such as pharmaceuticals or high-value ingredients. Additionally, there are pressure filling machines that utilize pressure to fill containers, which is particularly effective for carbonated beverages. Each type has its unique advantages, allowing manufacturers to choose the most suitable machine based on their production requirements.
For those dealing with viscous products, piston filling machines are highly effective as they can handle thick substances that may clog other types of machines. Meanwhile, automatic and semi-automatic filling machines are available for varying production scales, enabling businesses to optimize their operations based on demand. Understanding these different types of filling machines not only helps in selecting the right equipment but also plays a significant role in achieving greater efficiency and cost savings in industrial applications.
Mastering Industrial Filling Machines for Maximum Efficiency and Cost Savings
This pie chart illustrates the distribution of different types of industrial filling machines used in the industry, highlighting their market share and efficiency benefits.
Key Features to Look for in High-Performance Filling Equipment
When selecting high-performance filling equipment, several key features can significantly influence efficiency and cost savings in industrial settings. According to a report by Smithers Pira, the global packaging machinery market is projected to reach $50 billion by 2024, with filling machines representing a significant segment due to their crucial role in product packaging. Attention to specific features can maximize this equipment’s potential and minimize operational costs.
One pivotal feature to consider is the versatility of the filling machine. Equipment that can handle a variety of products, such as different viscosities and container types, helps streamline operations and reduces the need for multiple machines. This flexibility not only saves space on the production floor but also improves overall workflow and reduces downtime during changeovers. In a rapidly evolving market, this adaptability can provide a competitive edge.
Additionally, automation capabilities should be a primary consideration. Automation can greatly enhance the speed and accuracy of the filling process, which is critical in meeting production demands. A study by Allied Market Research indicates that the global industrial automation market is anticipated to grow significantly, emphasizing the value of integrating smart technology into filling operations. Machines equipped with advanced monitoring systems can detect inefficiencies in real-time, allowing for immediate corrective actions and further driving down operational costs.
Lastly, energy efficiency is another crucial feature to seek in modern filling equipment. With energy costs rising, using machines that consume less power while maintaining output can lead to substantial savings over time. According to a report from the International Energy Agency, enhancing energy efficiency in industrial processes can lead to a reduction in operating costs by up to 30%. Therefore, investing in high-performance filling machines that prioritize energy conservation is not only environmentally responsible but also economically advantageous.
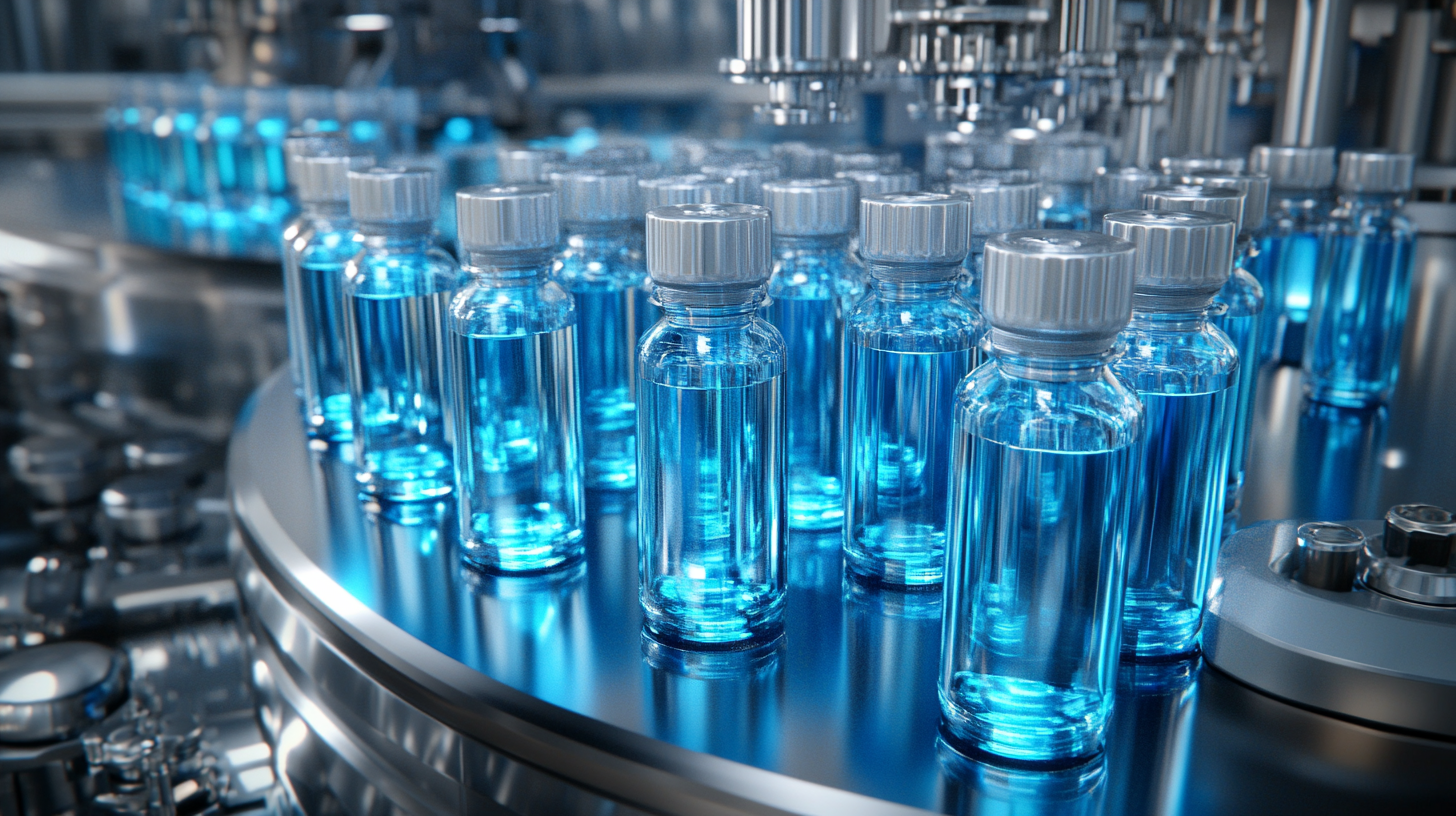
Strategies for Optimizing Filling Machine Efficiency
In the competitive landscape of industrial production, optimizing filling machine efficiency is paramount for improving operational output while minimizing costs. Industry reports indicate that manufacturers can achieve a 20-30% increase in productivity by implementing advanced filling technology and strategic process improvements. By focusing on key areas such as machine calibration, maintenance schedules, and operational training, companies can significantly reduce downtime and enhance throughput.
One effective strategy involves the regular calibration of filling machines to ensure accurate volume measurements. According to a study by the Packaging Machinery Manufacturers Institute (PMMI), deviations in fill levels can result in costly product waste, leading to an average loss of $30,000 per month for mid-sized companies. Incorporating sensors and automated feedback systems can mitigate these issues, allowing real-time adjustments and ensuring consistently high-quality fills.
Additionally, investing in staff training plays a crucial role in maximizing machine efficiency. A report by the National Association of Manufacturers reveals that organizations with comprehensive training programs see a 60% reduction in operational errors. By empowering employees with knowledge on best practices and machine functionalities, companies can foster a more proficient workforce capable of identifying inefficiencies and implementing immediate solutions.
Moreover, embracing preventive maintenance schedules is vital for safeguarding filling machines against unexpected failures. Research from the ReliabilityWeb indicates that companies practicing preventive maintenance can reduce machine breakdowns by up to 50%. This not only saves on repair costs but also enhances overall reliability, allowing businesses to maintain optimal service levels and cater to increasing market demands without interruption.
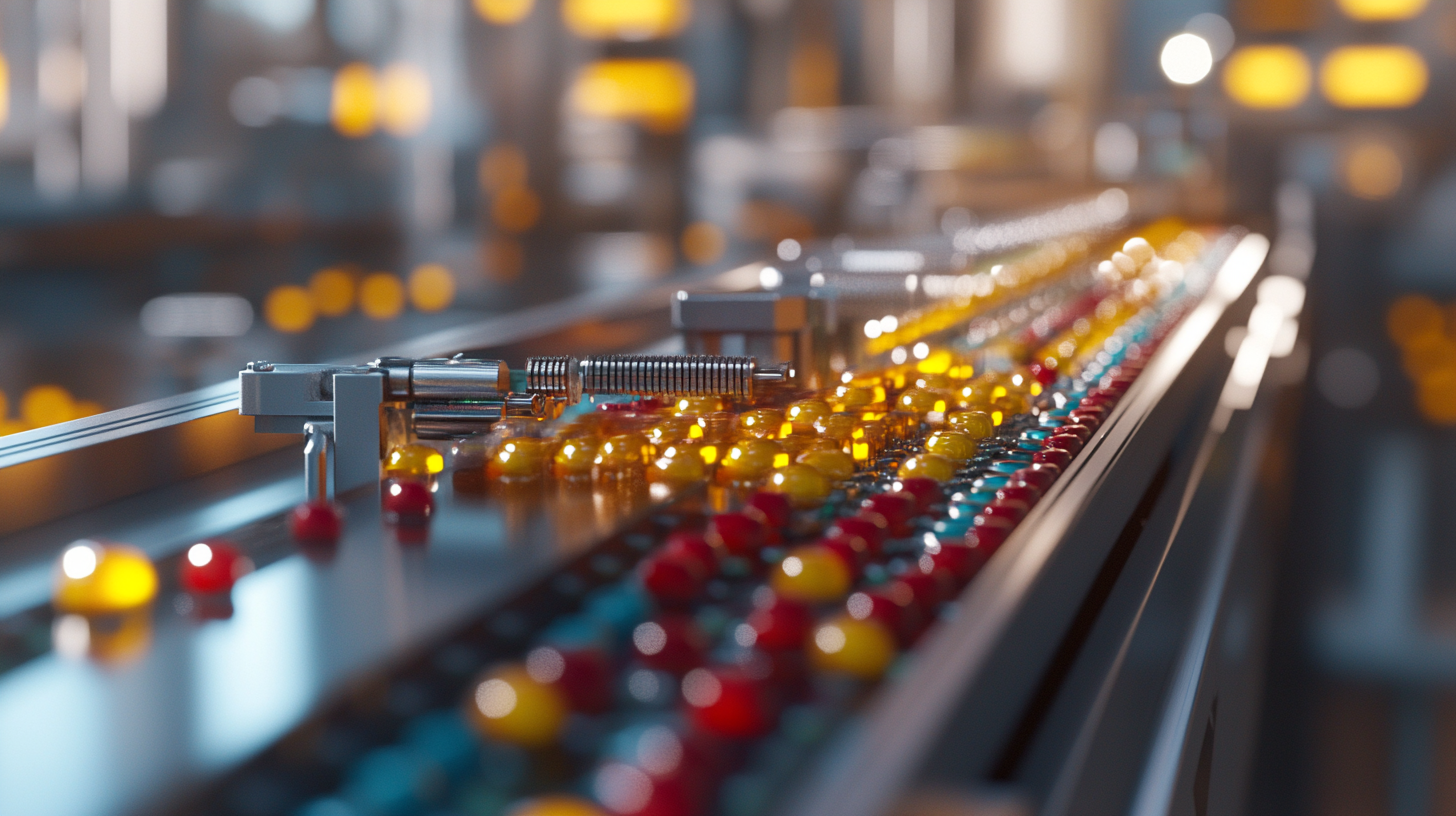
Cost-Benefit Analysis of Upgrading Filling Equipment
Upgrading your industrial filling machines can lead to significant cost savings and improved efficiency. A cost-benefit analysis is essential for any company contemplating this investment. Initially, evaluating the potential savings generated by increased production speeds and reduced labor costs is crucial. Modern filling machines are often designed with advanced technology that not only enhances speed but also accuracy, minimizing product waste and decreasing overall operational costs.
Moreover, consider the maintenance and downtime associated with older equipment. Frequent repairs and the potential for production halts can severely impact profitability. Newer machines typically require less maintenance and offer improved reliability, leading to higher uptime and consistent output. By analyzing the long-term operational costs related to maintenance versus the investment in new filling technology, companies can better understand the financial implications of upgrading.
Additionally, the flexibility of modern filling machines can be a game-changer. Many newer models can handle various sizes and types of containers, accommodating changing market demands without requiring extensive reconfiguration or lost production time. This adaptability not only supports current operations but also positions businesses to scale efficiently as market conditions evolve, further enhancing the cost-benefit outcome of upgrading filling equipment.
Mastering Industrial Filling Machines for Maximum Efficiency and Cost Savings - Cost-Benefit Analysis of Upgrading Filling Equipment
Parameter | Current Equipment | Upgraded Equipment | Annual Savings |
---|---|---|---|
Operating Efficiency (%) | 70% | 90% | $30,000 |
Machine Downtime (hours/year) | 200 | 50 | $15,000 |
Labor Costs ($/year) | $100,000 | $70,000 | $30,000 |
Initial Investment ($) | N/A | $150,000 | N/A |
Total Annual Profit ($) | $200,000 | $295,000 | $95,000 |
Maintenance Tips to Ensure Long-Term Reliability and Performance
Maintaining industrial filling machines is crucial for achieving long-term reliability and performance. Regular maintenance not only extends the lifespan of the equipment but also ensures that it operates at peak efficiency. One of the simplest yet most effective maintenance tips is to establish a routine inspection schedule. This should include checking for signs of wear and tear, ensuring that all components are functioning correctly, and identifying any potential issues before they escalate. Early detection can save manufacturers significant costs and downtime.
Another important aspect of maintenance is proper cleaning. Dust, residue, and product buildup can impede the machine's performance and lead to contamination issues. Implementing a thorough cleaning protocol after each production run will help maintain optimal filling accuracy and hygiene. Utilizing appropriate cleaning agents and following manufacturer guidelines can also prevent damage to sensitive parts, keeping the machinery in top condition.
Lastly, training staff on the correct usage and maintenance procedures is vital. Employees should be equipped with knowledge about the machines they operate, including troubleshooting common problems and understanding maintenance schedules. Investing in employee training not only helps in maintaining efficiency but also fosters a culture of safety and responsibility within the workplace, ultimately leading to a more productive and cost-effective operation.
Related Video
-
Manual vs. Automatic Drum Filling – Which Saves More Money?
View: 1328Channel: liquidfillingmachine#drum filling machine -
200L double filling machine equipment #automatic filling machine #200L 55Gallon packaging system
View: 120Channel: liquidfillingmachine#drum filling machine -
ibc tote filling systems#drum and tote filling systems
View: 34Channel: liquidfillingmachine#drum filling machine